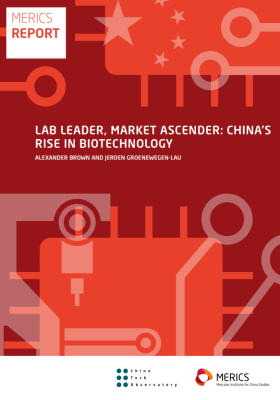
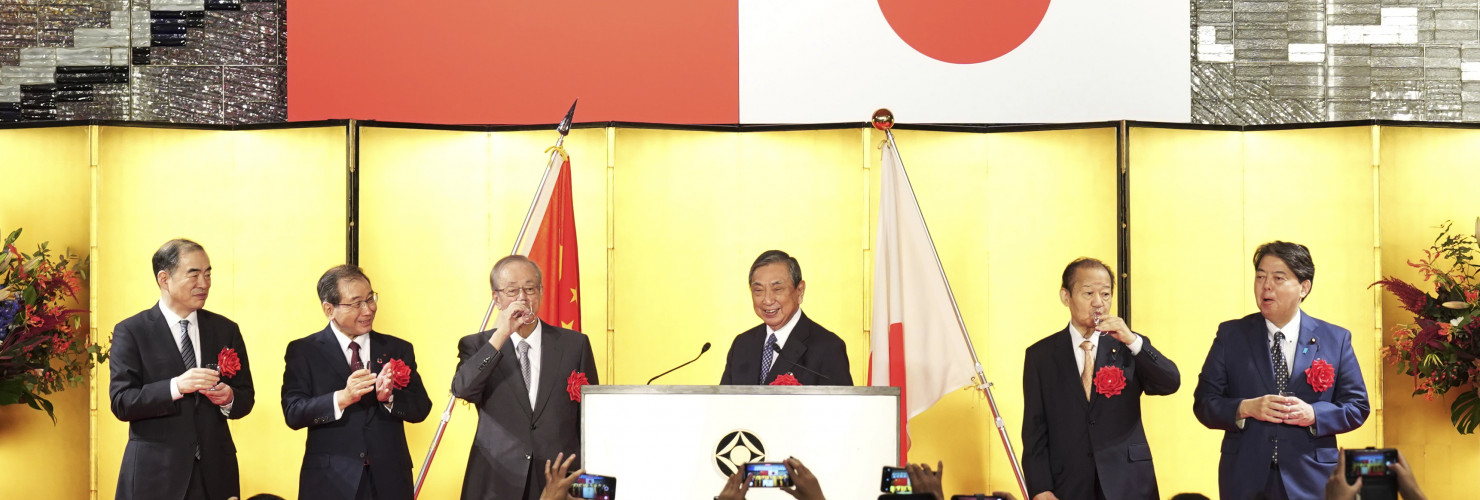
Japan’s Chinese lesson – diversifying only production is not enough
Europe lags behind Japan in managing economic interdependence with China. Aya Adachi and Koki Shigenoi say European companies have to look at sourcing.
The Russo-Ukrainian war and growing concern over Chinese intentions on Taiwan have triggered a serious discussion among European executives and policymakers about diversifying economic ties away from China, just as they are doing from Russia. Given the higher economic interdependence between Europe and China, European companies would be in a much more vulnerable position if they had to unwind business operations in China at the speed and severity with which they acted in Russia. Japanese companies have a similar problem, but have for a decade been pioneering ways to reduce economic dependence on their country’s big neighbor. Europeans could learn a thing or two from them.
The most important lesson: diversifying only assembly is not enough
The pandemic showed that moving manufacturing out of China means little if it continues to rely on Chinese inputs. Japanese companies began shifting production under the China Plus One strategy after China’s economic coercion over the Senkaku-Diaoyu islands disputes of 2010-2012. Labor cost increases, and growing political tensions, including the US-China trade war (2018-ongoing), were also drivers of this trend. But in 2021, Japanese manufacturers in the ten-nation Association of Southeast Asian Nations (ASEAN) still sourced 13.5 percent of raw materials and parts from China, slightly more than in 2016 (exhibit 1). (Companies operating in China sourced more than 90 percent of inputs locally or from Japan, making them less vulnerable to external shocks.)
As China’s Covid-19 lockdowns took hold in early 2020, these companies found their ASEAN manufacturing sites exposed to events in China. They learned that moving final production assembly from China would not cut dependence if they did not diversify their sourcing of input components at the same time. As European companies think more about manufacturing diversification, they should take note of Japanese companies’ painful experiences. Having moved production, companies could well encounter difficulties in securing new local inputs. Replacing Chinese supplies for production processes in ASEAN can be a challenge – but not doing so can undermine the aim of economic diversification.
ASEAN has become a preferred destination for companies shifting their manufacturing bases out of China. Flows of total foreign direct investment (FDI) into manufacturing in ASEAN increased almost threefold from 21,3 billion USD in 2016 to 62,1 billion USD in 2018.[1] This development was accompanied by increases in Chinese exports in intermediary products to ASEAN (see exhibit 2), indicating that Japanese companies are part of a broader trend. Companies should start thinking more about geopolitics and identify sources that are geopolitically less risky than China. But ASEAN remains intent on keeping Beijing on side – approach of avoiding choosing sides—or of “choosing both sides”— remains very popular.
An added problem for European companies is that Europe is only now starting to look at the supply-chain problem. The Japanese government, on the other hand, in 2002 began to strike trade agreements with most of its neighbors to promote economic diversification, maintain existing economic activities and better manage the unavoidable economic pull of the Chinese market. Initial pandemic-induced supply-chain issues of 2020 quickly subsided and required little further adjustment. But the Japan External Trade Organization and the Ministry of Economy, Trade and Industry still assessed this new vulnerability through various studies and published recommendations on how to deal with supply shortages.
The government also set up a 2.2 billion Yen (223 million USD) diversification fund in 2020 and an additional 2.1 billion Yen in 2021 to assist Japanese businesses in moving from China to Southeast Asia. For sure, as lockdowns returned to wide parts of China in 2022, prolonged shipping delays once again reminded Japan and the rest of the world of their continued reliance products made in China. But Japan is in a better position than most of them, also thanks to its recent Economic Security Law, which includes monitoring of and financial support for the supply of a range of critical items like semiconductors, batteries, certain minerals, machine tools, advanced materials, software, fertilizer and pharmaceuticals.
But diversification does not mean full-scale decoupling from China. Many Japanese companies will maintain their operations in China as long as they generate profits in local sales. Furthermore, cross-border production is vital for the region’s economies – and will likely strengthen after the recent conclusion of the Regional Comprehensive Economic Partnership, a fifteen-member free trade agreement between the ASEAN, Australia, China, Japan, New Zealand South Korea. Corporate diversification as well as government-led economic security measures show that Japan is aiming for a balanced, pragmatic, and geopolitically sustainable approach to managing its economic interdependence with China.
European companies are latecomers to a game in which Japan, China, and the US compete for ASEAN’s bestowal of lucrative trade and investment opportunities. While European companies might benefit from newly established local supply networks initiated by foreign rivals, they will also face difficulties in replacing Chinese intermediary products. Japan’s experience shows diversifying risks away from China is easier said than done. It is a long and gradual process that raises costs. But shifting assembly processes is a necessary step that must be followed by diversification of component sourcing. Difficult as it will be, European companies must assess their vulnerabilities and reduce their concentration of risk in China.